Quality at Batnon
At Batnon Precision Manufacturing, quality is not just a goal—it’s our commitment. We understand that our customers rely on us to deliver components that meet the highest standards of precision, reliability, and performance. That’s why we’ve developed a comprehensive quality management system designed to ensure excellence in every project we undertake.
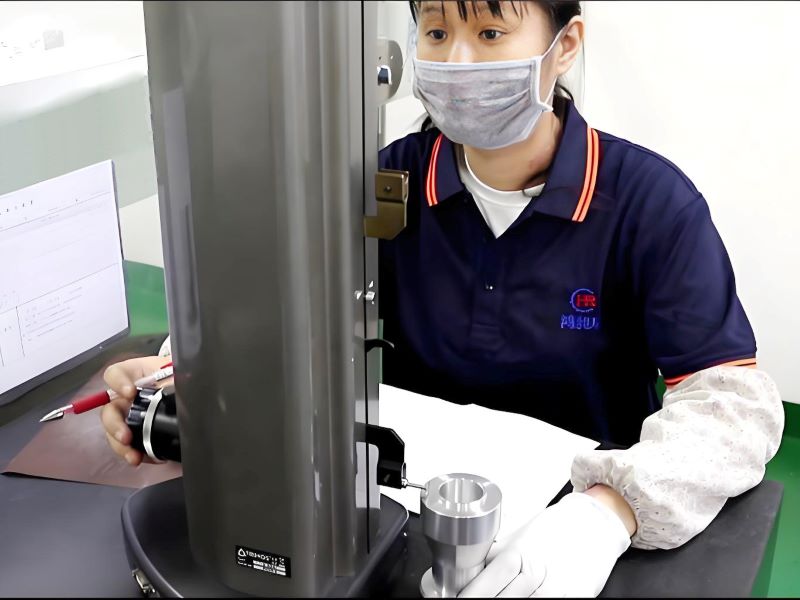
Our Quality Approach
At Batnon, quality starts at the very beginning of each project. We work closely with our customers to understand their specific requirements and ensure these are translated into every stage of production.
Design for Quality:
During the design phase, we use advanced CAD software to create precise and manufacturable components. We conduct rigorous design reviews to identify and address potential issues early.Precision Manufacturing:
Leveraging state-of-the-art machinery and skilled operators, we ensure every component is crafted with unparalleled accuracy.Proactive Quality Control:
Our team implements strict quality checks throughout the production process, preventing defects and ensuring consistency.Continuous Improvement:
We constantly evaluate and refine our processes to maintain high standards and adapt to evolving customer needs.
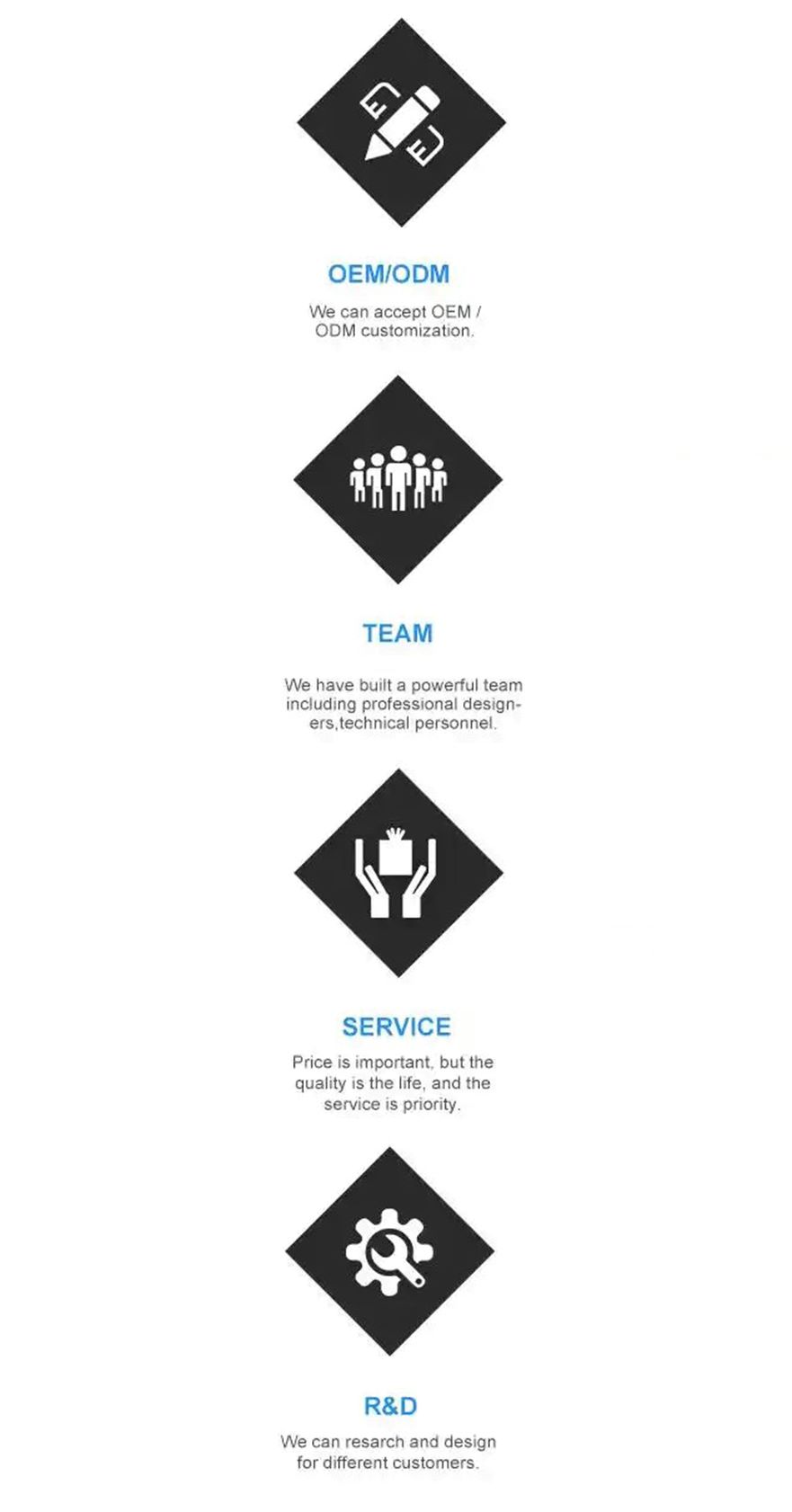
Inspection & Quality Control
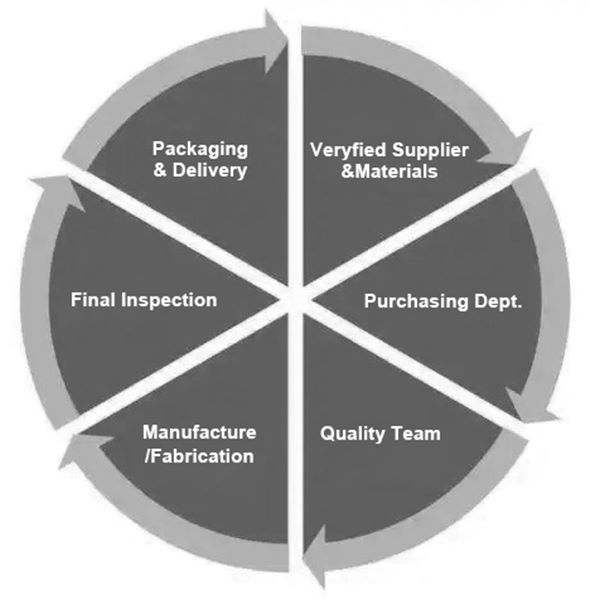
Our inspection and quality control processes are integral to ensuring that every part meets the required specifications.
Incoming Material Inspection:
All raw materials are inspected upon arrival to ensure they meet the necessary standards for production.In-Process Inspections:
During manufacturing, components are checked at critical stages to ensure dimensional accuracy and surface quality.Final Inspection:
Before delivery, each part undergoes a comprehensive inspection using advanced tools such as:- Coordinate Measuring Machines (CMM)
- Optical and laser measurement systems
- Surface roughness testers
- Micrometers and calipers
Quality Assurance
We are committed to delivering products that meet or exceed your expectations. Our quality assurance measures include:
ISO Certification:
Our operations comply with international quality management standards, ensuring reliability and consistency in every order.Traceability Systems:
Each component is tracked throughout the manufacturing process, providing complete traceability for materials and processes.Customized Quality Plans:
For each project, we develop tailored quality plans that align with your specifications and industry standards.
Why Our Quality Stands Out
Industry-Leading Standards:
With ISO-certified processes and state-of-the-art inspection equipment, we guarantee consistent quality for every part.Experienced Professionals:
Our team of engineers and quality specialists brings years of experience to ensure every detail is perfected.Advanced Tools & Technologies:
We use the latest inspection equipment and software to deliver precise, reliable results.Customer-Centric Focus:
Your success is our priority. We work closely with you to understand your quality expectations and ensure they are met at every stage.
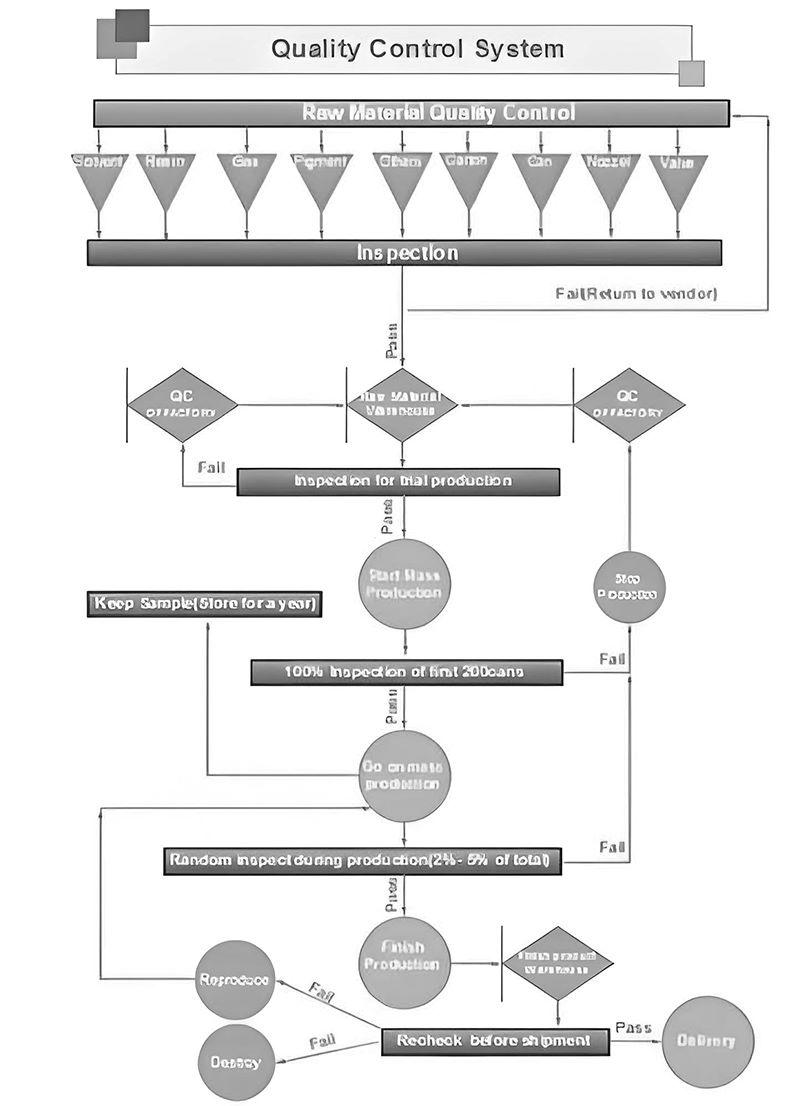
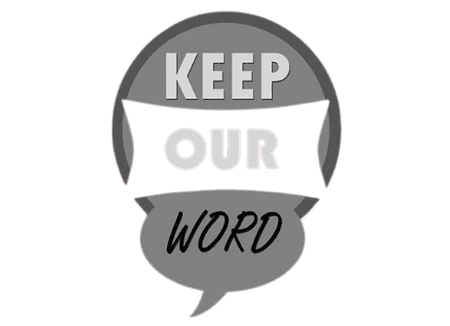
Our Promise to You
At Batnon Precision Manufacturing, we believe that quality is more than a benchmark—it’s the foundation of trust. By partnering with us, you can be confident that your projects will be handled with care, precision, and expertise. From design and production to inspection and delivery, our focus is on delivering excellence that supports your business success.
Incorporating Broader Capabilities
To complement our rigorous quality control, we offer a full range of precision manufacturing services, including:
- CNC Machining: High-precision milling, turning, and Swiss CNC turning for complex and accurate components.
- Plastic Molding: Scalable solutions for durable and custom plastic parts.
- Die Casting: Reliable metal components with superior strength.
- Extrusion Profiles & Sheet Metal Fabrication: Customized structural and industrial solutions.
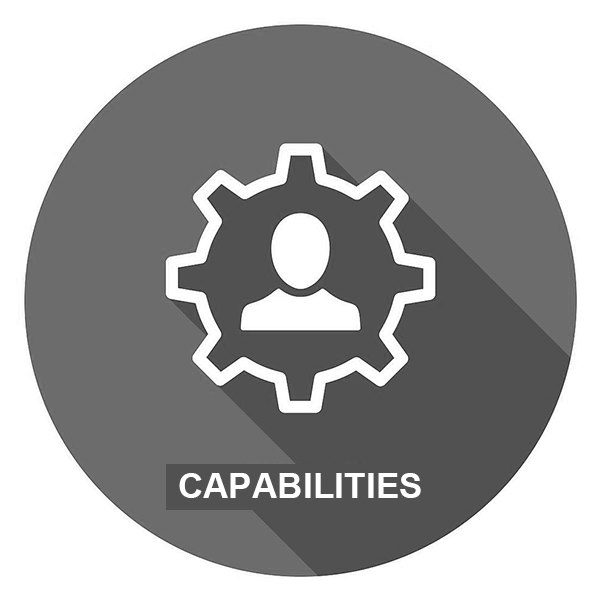
Applications of CNC Milling
Examples of Parts:
- Enclosures and housings
- Engine components
- Brackets and supports
- Precision gears and shafts
- Custom tooling
Customization Options:
- Milling of features like grooves, channels, slots, or intricate patterns for aesthetic or functional purposes.
Warranty
At Batnon, we stand by the quality of our products and services. To ensure your satisfaction, we offer the following policies:
Warranty Policy
Warranty Period:
We provide a 12-month warranty on all components and parts manufactured by Batnon, starting from the date of delivery.Coverage:
The warranty covers defects in materials, workmanship, and functionality under normal use and proper installation.Exclusions:
- Damage caused by misuse, improper handling, or unauthorized modifications.
- Wear and tear due to normal use or exposure to extreme conditions.
4. Claim Process:
- Contact our customer support team with your order details and a description of the issue.
- We may request photos or the return of the defective product for assessment.
- If approved, we will repair or replace the defective item at no cost.
Have an Ongoing Project? Try How We Can Help!