Service - Product Design Services
About Product Design Services
At Batnon, we specialize in bringing ideas to life through our comprehensive product design services. Our expertise encompasses New Product Development (NPD) and Industrial Design, ensuring that your concepts are transformed into innovative, market-ready products. With a focus on creativity, precision, and functionality, we leverage our “Integrated Process” approach to deliver exceptional results.
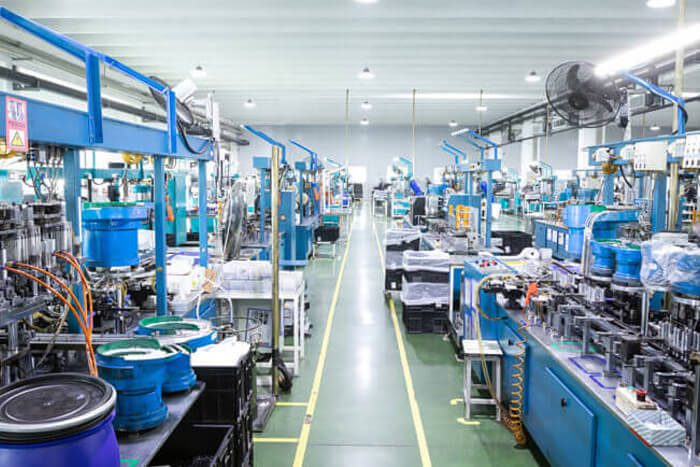
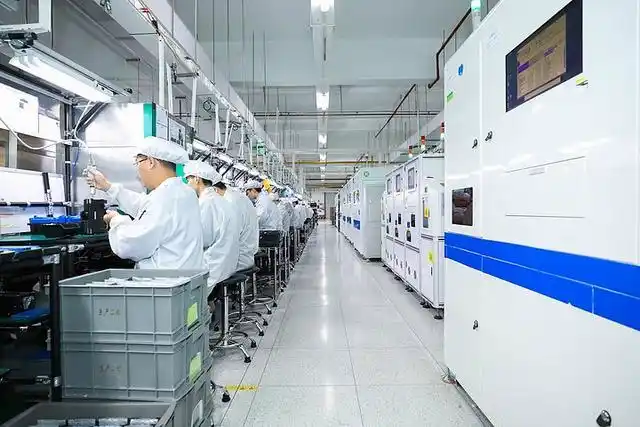
New Product Development
New Product Development (NPD) at Batnon is a structured yet flexible process designed to turn concepts into high-quality products efficiently and cost-effectively. Here’s how we do it:
1. Ideation and Concept Development
Brainstorming: Collaborating with clients to explore innovative ideas.
Market Research: Analyzing industry trends and consumer needs to refine concepts.
Feasibility Studies: Evaluating technical, financial, and logistical viability.
2. Prototyping and Testing
Rapid Prototyping: Using CNC machining, 3D printing, and other technologies to create functional prototypes.
Iterative Testing: Conducting performance, durability, and usability tests to refine the product.
Feedback Integration: Incorporating client and user feedback for continuous improvement.
3. Development and Production Readiness
Design for Manufacturing (DFM): Ensuring designs are optimized for efficient production.
Material Selection: Choosing the best materials for quality, cost, and sustainability.
Production Planning: Developing timelines and workflows for seamless production.
4. End-to-End Support
Documentation: Providing detailed specifications, blueprints, and compliance records.
Launch Assistance: Supporting product introduction with marketing and logistical insights.
Industrial Design
Industrial design at Batnon combines aesthetics, functionality, and innovation to create products that stand out in the market. Our design philosophy ensures that every product is visually appealing, user-friendly, and aligned with client goals.
1. Design Principles
User-Centric Approach: Prioritizing user needs, comfort, and accessibility.
Sustainability: Incorporating eco-friendly practices and materials.
Ergonomics: Designing products for optimal usability and interaction.
2. Design Process
Concept Sketching: Creating initial designs and visual representations.
3D Modeling: Using advanced CAD software to develop detailed models.
Design Validation: Testing designs for functionality, aesthetics, and feasibility.
3. Collaboration and Customization
Client Involvement: Working closely with clients to ensure designs align with their vision.
Customization: Offering tailored solutions for unique market demands.
4. Integration with Manufacturing
Prototyping: Ensuring seamless transition from design to production with functional prototypes.
Material Feasibility: Selecting materials that balance design integrity with cost-efficiency.
Production Alignment: Collaborating with manufacturing teams for consistent results.
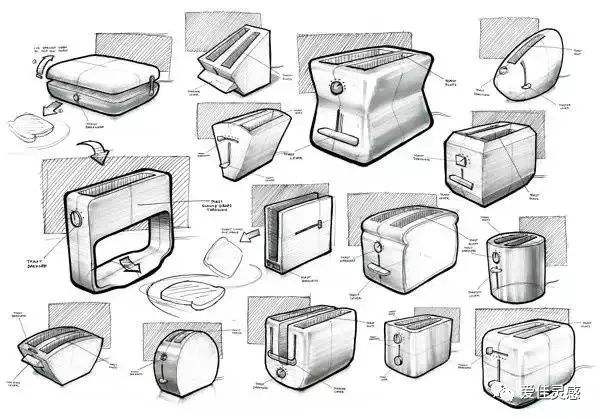
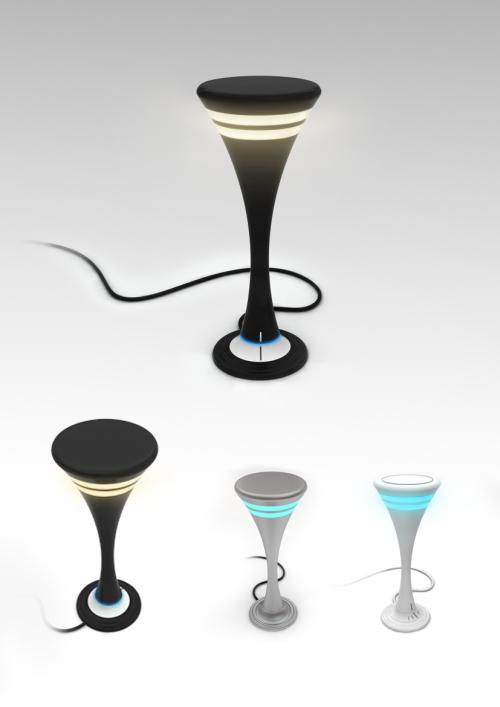
Why Choose Batnon for Product Design?
1. Comprehensive Expertise
Our team of designers and engineers excels in both creative and technical aspects, ensuring well-rounded solutions.
2. Integrated Process
We combine advanced technologies, skilled labor, and efficient workflows to deliver high-quality designs and products.
3. Client-Centric Approach
We prioritize client goals, ensuring that every design reflects their vision and meets market demands.
4. Cost-Effective Solutions
By streamlining processes and optimizing resources, we deliver premium designs without breaking the budget.
5. Sustainable Innovation
We integrate eco-friendly practices into our design and development processes, contributing to a greener future.
Case Studies
Case Study 1: Consumer Electronics Design
Developed a sleek, user-friendly electronic gadget that achieved market success through innovative features and ergonomic design.
Case Study 2: Industrial Equipment Redesign
Redesigned a complex industrial machine for improved efficiency, safety, and aesthetics, reducing production costs by 25%.
Case Study 2: Large-Scale Mechanical Assemblies
Our team handled the assembly of industrial machinery components, maintaining 100% accuracy across thousands of units.
How We Innovate in Product Assembly
Continuous Improvement: Investing in R&D to stay ahead of industry trends.
Workforce Development: Training programs to enhance team expertise.
Client Collaboration: Partnering with clients to align our processes with their goals.
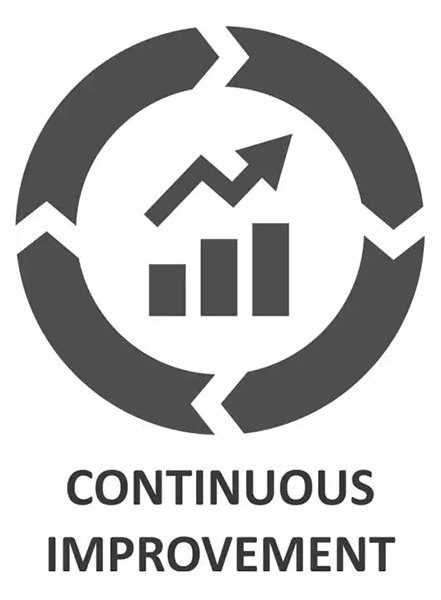
Ready to streamline your product assembly process? Contact us today to learn more about our services and how we can bring your ideas to life efficiently and effectively.